The Future of Clean Manufacturing according to the DOE’s Industrial Demonstrations Program
The DOE's Industrial Demonstrations Program offers valuable insight into the future of industrial decabonization technologies. Identifying emerging trends and notable gaps among the selected projects will inform industrial decarbonization policy in the coming years.
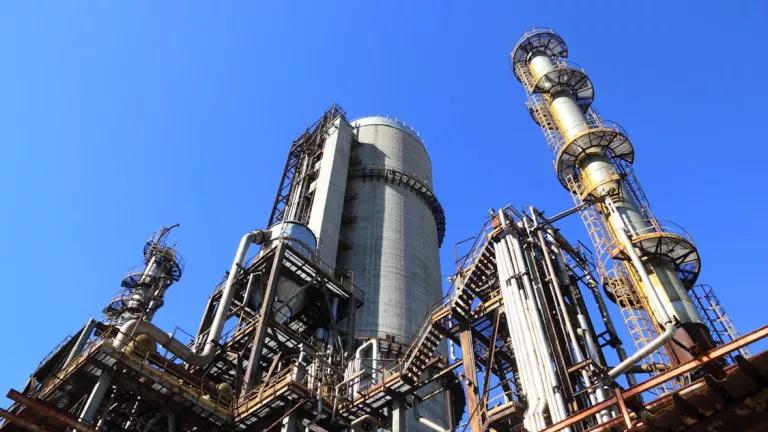
The U.S. Department of Energy’s Office of Clean Energy Demonstrations (OCED) rolled out one of the largest federally funded climate programs in history earlier this year. With funding from the Biden-Harris administration’s Bipartisan Infrastructure Law (BIL) and Inflation Reduction Act (IRA), the new program, called the Industrial Demonstrations Program (IDP), tackles the notoriously emissions-intensive industrial sector.
Decarbonizing heavy industry is immensely important. It is not only a top priority for meeting climate goals, since industry lags behind other sectors in terms of reducing carbon emissions, but it can also accomplish important economic and environmental goals, like modernizing American manufacturing and addressing localized air pollution. We’ve previously written about the IDP’s formation and explained how the funding process will play out over time. Now, we take a closer look at the projects, identifying trends that will inform industrial decarbonization policy in the coming years.
Diversified bets: IDP’s approach to innovation
Before diving into the projects, it helps to put the IDP in the context of other major clean energy programs. With $6 billion in funding, the IDP is the third-largest program funded by OCED, which manages a portfolio of about $26 billion from the BIL and IRA. The IDP follows closely behind the Hydrogen Hubs ($8 billion) and Carbon Management ($7 billion) programs, but unlike those, which are dedicated to specific emerging climate solutions, the IDP spans the existing industrial sector, funding projects across multiple manufacturing industries to demonstrate a range of novel decarbonization approaches and technologies at scale. Its approach is to co-fund with private industry a diversity of projects and technologies with the goal of finding successful formulas and setting the stage for industry-wide adoption in the future.
Emerging themes and trends
In total, there are 33 projects across eight industry groups.
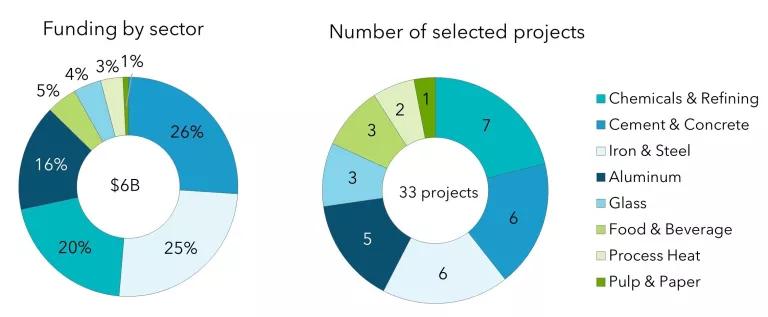
After categorizing each of the projects by the decarbonization levers used—e.g., electrification; energy efficiency; carbon capture, utilization, and storage (CCUS), etc.—we found common themes among industries, promising trends, and notable gaps in funding where there is room for future investment.
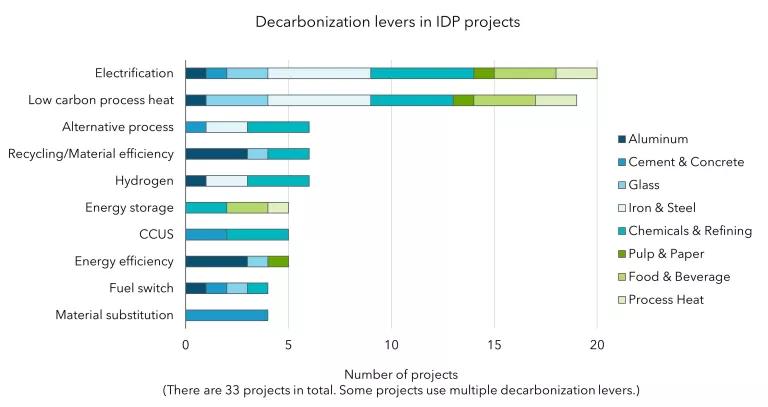
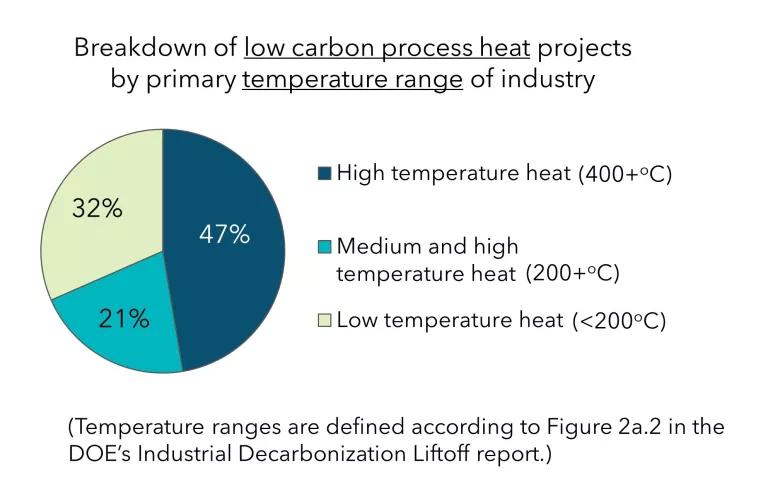
- Electrification is present across all eight industries, although in different forms and not without challenges.
- Twenty of the 33 projects include some form of electrification to decarbonize, mostly through the installation of direct electric technologies, such as electric furnaces or heat pumps. Some of the projects, however, rely indirectly on electrification. Namely, three require electrolytic hydrogen as a feedstock, four use electricity to charge energy storage systems, and a new aluminum smelter intends to rely on carbon-free electricity.
- Beyond carbon emissions, electrification also stands to reduce criteria air pollutants, which is particularly beneficial in communities overburdened by pollution.
- Despite its prevalence, electrification in industry faces a number of challenges: the need for reliable, continuous, affordable, and clean electricity and the typically higher baseline costs of electricity compared to current fuels. It’s likely that additional policy support will be needed to address such challenges and ensure the long-term adoption of electric technologies in a period of load growth.
- More than half of the projects tackle emissions from process heat, the largest source of industrial emissions.
- Process heat is the thermal energy used to transform materials into manufactured products and refers to any technology that provides heat (e.g., boilers, furnaces, kilns, ovens). Currently, the majority of process heat systems rely on fossil fuels.
- Of the 19 projects targeting process heat, most plan to switch from fuel combustion to electric technologies like electric furnaces, electric boilers, heat pumps, and membrane separations. Four projects will use thermal energy storage, charging “heat batteries” with low-cost electricity and storing heat at temperatures above 1,000 degrees Celsius. One will use battery energy storage for electric heating.
- Thirteen of these projects are in primarily high-temperature (greater than 400 degrees Celsius) or medium- to high-temperature (greater than 200 degrees Celsius) industries, challenging the notion that it’s hard to decarbonize high-temperature heat.
- The relatively few applications of CCUS and hydrogen projects suggest that they are likely essential in certain cases but far from universal in their suitability and attractiveness for decarbonizing industry.
- Notably, two projects deploy CCUS to address emissions from the cement industry, where carbon dioxide forms as a by-product in the current process. A few projects in chemicals and refining include CCUS with the carbon dioxide subsequently used as feedstock for primary chemicals production.
- Hydrogen is also used as a decarbonization lever in only select applications. Its use is mostly as feedstock for chemicals or in direct reduced iron production for steel, as opposed to inefficient end uses, such fuel blending in furnaces.
On the horizon for industrial decarbonization
While the IDP is just one step toward severely needed investment in the industrial sector, the trends across projects show where there is momentum and where there are gaps. Clearly, future investment in industrial decarbonization is headed toward broad electrification, especially for heat. Energy storage is another growth area that could also solve some of the main challenges with industrial electrification, like continuous energy supply and reliability.
On the other hand, a major gap among IDP projects is eliminating process emissions. Only four projects deal with process emissions (two in cement, one in steel, and one indirectly in chemicals). This is not entirely surprising because the IDP is designed to fund technologies with high technological maturity, but the gap suggests that more research, development, and demonstration investments could be made in advanced technologies tackling process emissions, such as molten oxide electrolysis for iron and steel and pre-calciner capture for cement. Another area lacking in the IDP and ripe for future funding is electrification of the most emissions-intensive processes. These could include electric kilns and pre-calciners for cement as well as electric steam crackers for chemicals.
For now, the IDP has provided a much-needed spark for industrial decarbonization. We plan to stay engaged as projects develop, especially as they impact communities, and build the case for future investments.